By Joseph Palmersheim
When Metro Maintenance’s old tunnel washer got damaged during a washing project two years ago, the road ahead was somewhat unclear.
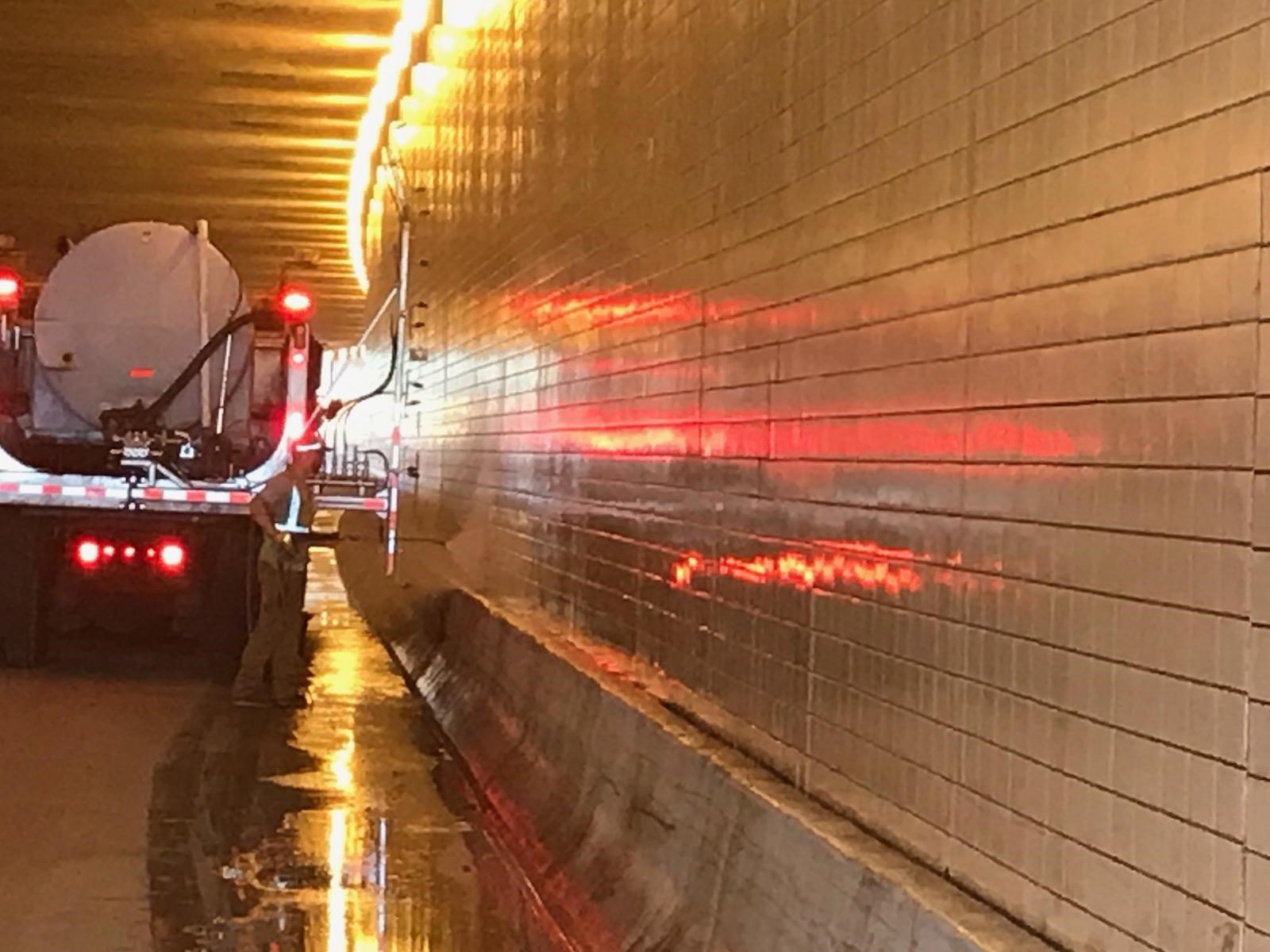
District 1's tunnel washer at work in the tunnel through downtown Duluth. The unit consists of a spray washer arm mounted where a wing blade usually goes on a plow truck. Photo by Nathan Smith |
The washer, built in 1996, wasn’t supported for parts or service anymore. Buying a new one was “an equipment budget buster,” said John Bieniek, Metro District Maintenance Operations engineer. The district resorted to outsourcing the tunnel-washing work to contractors. These cleanings, which cost around $85,000 per event, took place in fall 2019 and spring 2020. The contractors did not perform the traffic control or site cleanup, so Metro still needed to provide all of the supporting activities on those washes.
Facing a similar issue, District 1 took a different path, building its own tunnel washer last spring. The unit consists of a spray washer arm mounted where a wing blade usually goes on a plow truck. Water comes from an 1,800-gallon tank mounted in the truck’s bed. Nate Smith, Virginia shop supervisor, said the idea came from Dave Ivers, Metro District’s superintendent of Fleet Equipment, who found that the Colorado DOT had built something similar.
“We took what Colorado built and made a high-pressure, low-volume version,” Smith said. “We built one for about $6,000. I came up with the design and Nick Daronco, heavy equipment mechanic, developed the system and put it together for us.”
District 1’s machine was tailor-made for the tunnels in that area, Smith said, with spray going up about 12 feet. The nozzle assembly can rotate to spray on either side of the truck. When it was first used in May, tunnel cleaning was cut from three days to one, in part because the new machine only took up one lane of traffic.
“Our design was really simple, as simple as possible,” he said. “It’s like a car wash, but instead we made it mobile.”
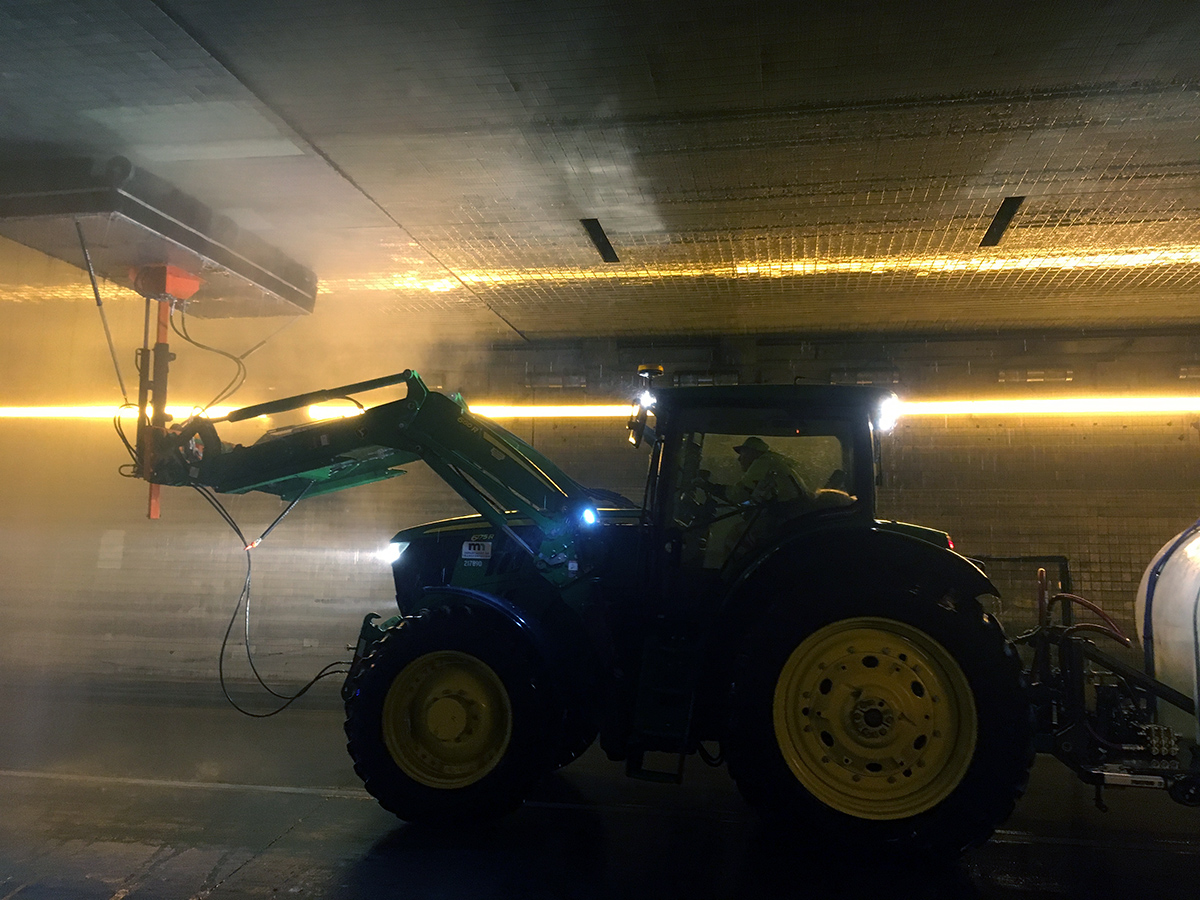
Metro District's tunnel washer is mounted on a John Deere tractor. The washing equipment can be removed, freeing the tractor up for other duties. This photo was taken during a cleaning of the Lowry Hill Tunnel on Oct. 21. Photo by John Bieniek |
Based on the success and the low development cost of the District 1 machine, Metro District launched its own project to build a tunnel washer. The project was assigned to the Maple Grove mechanic shop and included in-house project management, supervision, mechanics and welders, along with maintenance field staff and consultation with District 1 staff. Joe Johnson, Transportation Operations supervisor (Work-Out-Of-Class), served as the project manager. Work started in July and wrapped up in October.
Unlike District 1’s washer, Metro District’s washer had to be able to wash ceilings. As a result, it too is tailor made for the tunnels it needs to clean. The washer is mounted on a John Deere tractor, the same kind used for mowing and maintenance. A steel deck pump mount was added to the rear of the tractor, which tows a trailer with a 1,000 gallon water tank. The trailer, fabricated by MnDOT, has swivel tires on it so it can be backed up and turned within the width of the highway. The washer assembly is mounted on the front of the tractor. Its 10-foot-by-5-foot washer head has a series of jets that shoot water under pressure, with small wheels that ride the wall or ceiling surface, ensuring that the jets don’t touch what they are washing.
“The washer can swivel to the right, straight up or to the left,” Bieniek said. “It’s able to rotate to go on either wall. With the wheels, this thing is basically touchless.”
The project goal was to have Metro’s new tunnel washer ready to do the semi-annual Lowry tunnel cleaning this October and to not purchase any contracted services, Bieniek said. The new washer was tested Oct. 13 in the tunnel on Hwy 55 near the airport in Minneapolis, and tested again Oct. 19 after pulley adjustments. The results of that test were good and the adjustments to the machine held up well, Bieniek said. With that, the machine was deemed ready for Lowry Hill Tunnel, with its District 1 cousin there on standby in case the need arose.
The westbound portion of the Lowry Hill Tunnel was washed Oct. 21. Light illuminance readings from the tunnel walls were taken before and after those washings, and will be compared to the results obtained by the contractor’s machine last spring. A wash scheduled for Oct. 22 was cancelled due to weather. As MnDOT was doing the work instead of a contractor, this was “no big deal,” Bieniek said.
“From the preliminary measurements that we took, the new washer got the tunnel cleaner than the contractor did, while using less water,” Bieniek said. “Thanks to this, we have a cleaner tunnel, we use less water, we have more scheduling flexibility, and a lower cost.”
Bieniek noted that water used to clean the Lowry Hill Tunnel isn’t allowed to go down the drain. The drains are plugged in advance, and the dirty water is collected and driven to a water treatment facility.
Both of these tunnel washers are removable from the vehicles they have been paired with, meaning that they can be used for typical duties when tunnel washing isn’t needed, or when the vehicle needs to be updated.
Metro’s tunnel washer project cost around $40,000 – far less than a purpose-built tunnel washer.
“It wouldn’t make sense spending a couple hundred grand with a brush,” Smith said. “Some of those machines cost $800,000, and only one company in Europe makes them. You’d be using it for about two weeks a year. Both Metro’s tractor and my truck get put back in the fleet. The utilization on both of those piece of equipment went way up by adapting them to do a different job.”
Bieniek was pleased with how everything went.
“I am extremely impressed, proud and happy with the results of this metro project,” he said. “District 1 was super important in this. This is a great effort between the mechanic and maintenance area. The mechanics built it for the needs of maintenance, and both parties were involved in the development. It’s a real nice combination of internal staff and a low cost.”
|