By Sue Roe
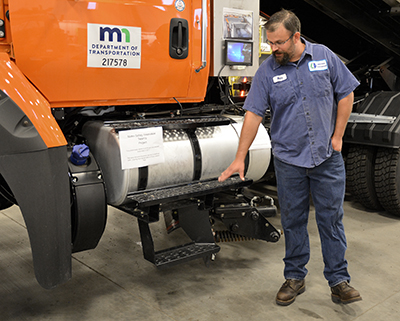
Nate Smith, Maple Grove truck station heavy equipment mechanic, shows the steps that are used to get in and out of a truck. The Safety Innovation Team designed the lower step to make it easier and safer for employees to enter and exit the truck. Photo by Sue Roe |
There’s a team at the Maple Grove truck station quietly making the workplace safer for maintenance employees and the traveling public.
“We work on spotting things that could be safer and easier to do,” said John Bieniek, Metro District maintenance operations engineer. “This group is empowered to come up with solutions. We get a lot of energy from each other.”
The group, known as the Metro Safety Innovation Team, meets monthly to discuss their ideas. Besides Bieniek, the team includes a heavy equipment mechanic, a welder, two safety employees, one mechanic supervisor, a maintenance worker and two maintenance supervisors. Nate Smith, mechanic; Duane Klein, welder; and Doug Thies, Metro District safety administrator, created the group.
“The meetings are a big brainstorming session and everyone is equal and that’s what makes it work,” said Julie Libonate, Metro District safety services supervisor.
The first innovation came after employees were at risk of being injured getting in and out of redesigned snowplows. Air emissions standards require MnDOT to install exhaust equipment under the truck. That requires the fuel tank to be raised, which increases the truck’s height and makes the step to get into the truck higher, increasing the risk of a trip or fall. The team created a lower step that bolts on the truck. The original step remained, but now employees use two steps to get into the truck.
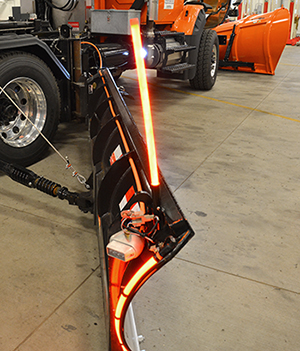
This is the lighted wing plow marker the Metro Safety Innovation Team created to make the wing more visible to the traveling public and snowplow operators. The marker will also be used on snow blowers this winter. Photo by Sue Roe |
The step innovation caught on and expanded to statewide use in 2017. Central Shop employees refined the step design and now install it on all new trucks. It can also be purchased by districts from a contractor that makes it.
“It accommodates someone who is shorter really well,” said Smith, who built the step with Klein. “Employees often get in and out of a truck 30 times a day.”
Kyle Lundberg, transportation generalist at Maple Grove, asked the team to figure out a way to make the snow blower, which blows snow from the roadway into the back of a truck, more visible on the roadway. Smith got LED rope lights, inserted them into a flexible nylon tube and inserted the tube into a two-foot translucent neon orange tube to make a lighted plow marker.
“When the plow truck is trying to line up with the blower, the driver can’t see the end of the truck very well,” said Smith. “Sometimes the two trucks collide and that affects the life of the truck.”
The lights will also be used on a snowplow wing tip to increase wing visibility at night for the traveling public, which can help avoid rear-end crashes, and for snowplow operators to see placement in relation to guardrails.
Smith said the lights will be tested on several wing plows and snow blowers this winter. Cost for the light is about $30 a pair. A vendor’s cost is between $130 and $140, but Smith said they don’t work as well because they’re made of fiberglass and don’t emit enough light.
When Smith learned that employees sustained injuries when clearing the auger that moves salt from the truck to the spinners, he crafted an automatic shut off system by adapting the wiring. The system stops all spreader operations when the truck is placed in park.
“By installing this system, we reduced the chances of an operator coming into contact with the rotating auger shaft,” said Smith.
That solution was created using a wire that costs one dollar and a diode that costs three cents.
Metro District will modify the augers on all its trucks over time and is working on statewide implementation.
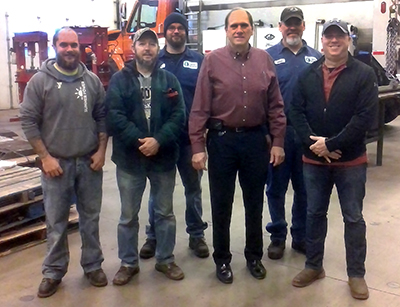
The Metro Safety Innovation Team includes (from left) Dan Backsen, Jason Novak, Nate Smith, John Bieniek, Duane Klein and Jeremy Gjovik. Not shown are Julie Libonate, Doug Thies and Mike Waters. Photo by Rickiesha Grant |
This winter the team will test a way to keep snow off the wiper blade. Snow often turns into ice below the wiper creating an “ice dam.” Snowplow operators have to get out of the truck to remove it. Installing a piece of metal on the hood that causes air to deflect from the wipers will prevent snowplow operators from having to get out of the truck, saving time and avoiding the risk of a fall.
“The team works on ideas that make sense,” said Thies. “The smallest of ideas we make a reality. Nate does a good job of coming up with what we need and then Duane welds it. We can dream up some pretty significant things, but if it isn’t economical or feasible we aren’t going to do it.”
Libonate said the innovations bring safety to the forefront.
“There were four injuries last year where employees got their hand in the auger. This invention helps us avoid catastrophic injuries. There are many incidents involving the plow wing. The lights will help reduce these numbers. We’re reducing injuries and that’s the ultimate goal,” she said.
The group just launched a website that shows the agency’s innovations and encourages districts to share their ideas.
“The exciting thing about the safety innovation team is that it’s still just the beginning,” said Thies. “Imagine what it’s going to be like when employees can go to the website and say ‘Here’s my idea.’” |