|
|
|
 |
TABLE of CONTENTS |
Innovative technology reduces time to replace Larpenteur Avenue Bridge |
By Rich Kemp
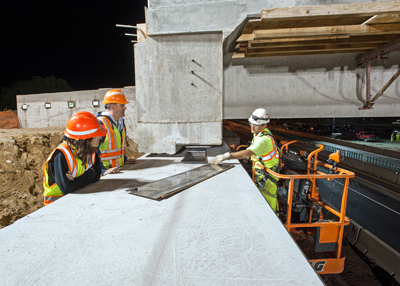
Nancy Daubenberger, state bridge engineer, and Dave Herzog, project manager, discuss the Larpenteur Avenue Bridge slide with a contractor during the beginning stages of the bridge placement July 10. Photo by David Gonzalez |
The Metro District, with guidance from the Bridge Office, used a new technique that cuts construction time in half, reduces impact to traffic and businesses, and improves safety. The new technology, known as slide-in-bridge construction, was used to move the Larpenteur Avenue Bridge into place July 9-10.
Rebuilding a bridge can take many months. During a typical bridge construction project, the bridge abutments and piers are constructed first and the bridge beams and deck are formed and cast directly on the support structures. Depending on the complexity of the bridge, this method of rebuilding a bridge can take many months.
“Performing the bridge slide allowed the contractor to reduce the time Larpenteur Avenue was detoured by over 60 days as compared to conventional construction methods,” said Dave Herzog, project manager.
The Larpenteur Bridge beams, deck and support structures were constructed simultaneously. The beams and deck were built on a temporary structure just four feet north of the existing bridge that was still open to motorists. After the concrete deck was poured and while it was curing, crews demolished the existing bridge, and immediately started rebuilding the support structures for the bridge spanning I-35E.
Simultaneously constructing the bridge beams, deck and supports accelerates the bridge construction process, and reduces the time the road is closed.
Hydraulic jacks were used to slide the 3.5 million pound bridge beams to their permanent location. The SIBC method only moves the bridge laterally (in a straight line). It is a lot less complicated and is typically used when the bridge deck is constructed within feet of the existing bridge. The bridge beams were constructed on a solid concrete “sliding shoe.” The shoe provides a surface to safely push the bridge. Teflon pads placed under the shoe create a frictionless surface which allows the bridge to slide.
To help with the slide, the crew used a household item that you wouldn’t expect to see on a bridge construction project.
“When sliding the first 10 feet, the contractor used 100 percent of the calculated capacity of the pumps, said Dave Herzog, project manager. “After that, the contractor started using liquid dish soap to further reduce friction and the pumps operated at 25 percent of the calculated capacity."
For the Larpenteur Bridge move, crews closed I-35E in both directions between Wheelock Parkway and Larpenteur Avenue from 10 p.m. through 5 a.m. for two nights.
“We consider the slide-in to be a success,” said Tony Lesch, design build principal engineer. “There were some challenges, and the actual slide-in took a bit longer than anticipated. But the fact is, we were able to safely put a bridge deck in place that wasn’t there two days before that.”
Watch a time lapse video of the video slide process.
The bridge slide is part of the I-35E MnPASS project, which includes adding a MnPASS Express Lane between Cayuga Street and Little Canada Road, improving the pavement on I-35E and replacing the Arlington Avenue, the Wheelock Parkway, the Larpenteur Avenue bridges and the I-35E bridges spanning local roadways. Read more about the MnPASS project by visiting www.mndot.gov/metro/projects/35estpaul/mnpass.html.
|
 |
|
|
 |
TABLE of CONTENTS
 |
Construction begins on historic Hwy 43/Winona Bridge project |
By Mike Dougherty, District 6 public affairs coordinator
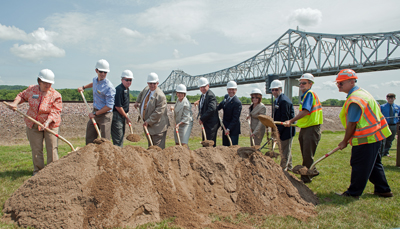
Officials broke ground for the Hwy 43/Winona Bridge project July 18 in Winona. From left, Judy Bodway, Winona city manager; state Sen. Jeremy Miller of Winona; state Rep. Gene Pelowski of Winona; Winona Mayor Mark Peterson; U.S. Sen. Amy Klobuchar; U.S. Rep. Tim Walz; MnDOT Commissioner Charlie Zelle; Winona Chamber of Commerce President Della Schmidt; MnDOT District 6 District Engineer Jeff Vlaminck; Ames Construction Vice President Jerry Volz; and Winona Bridge Project Engineer Terry Ward. Photo by David Gonzalez |
Federal, state and local officials broke ground in Winona July 18, signaling the start of the five-year, $162 million Hwy 43/Winona Bridge project.
Nearly 100 people attended the celebration, which featured Commissioner Charlie Zelle, U.S. Sen. Amy Klobuchar, Congressman Tim Walz, state Sen. Jeremy Miller, state Rep. Gene Pelowski and Winona Mayor Mark Peterson, who emceed the event.
“This project is noteworthy for many reasons, particularly because it preserves the historic bridge for future generations while building a new river crossing to connect the thriving communities on both sides of the Mississippi River,” said Zelle.
“The Winona Bridge project is also the first time MnDOT will use the construction manager-general contractor method of delivery, an innovation that allows us to save time, improve cost control, optimize the schedule and enhance collaboration between MnDOT and the contractor,” he said.
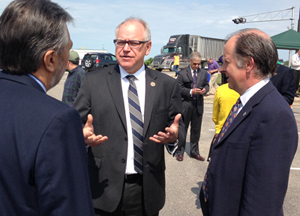
U.S. Rep. Tim Walz, center, discusses transportation issues with Jeff Vlaminck, District 6 engineer, and Commissioner Charlie Zelle during the groundbreaking ceremony for the Hwy 43/Winona Bridge project July 18 in Winona. Photo by Kevin Gutknecht |
MnDOT will build a new bridge to the north of the existing bridge, with anticipated completion in fall 2016. Crews will then repair and reconstruct the existing bridge, which is expected to be finished by fall 2019. Go to the project website to see a simulation of the completed bridges.
Already this week, crews have begun installing a floating silt curtain along the shoreline in preparation for removing trees from Latsch Island. In addition, the steel sheeting that will be used to build barge docks is being loaded in Dresbach and moved upriver by barge to Winona.
Built in 1941, the Hwy 43/Winona Bridge carries an average of 11,300 vehicles per day between Minnesota and Wisconsin. It is one of 172 bridges identified as part of the 2008 Trunk Highway Bridge Improvement Program.
For more information about the construction manager-general contractor approach that the Minnesota Legislature authorized in 2012, see www.mndot.gov/const/tools/cm-gc-overview.html.
|
 |
|
|
 |
TABLE of CONTENTS
 |
Enhancing Financial Effectiveness progress reports are posted to EFE website |
By Mary McFarland Brooks
The progress of the Enhancing Financial Effectiveness effort was documented on July 14 with PowerPoints from the four Battle teams, detailing their successes and challenges since the previous April 2014 update.
The Battles are:
- Asset management
- Financial management
- Information and outreach
- Project management
One of the outcomes of the Information and Outreach battle in the last quarter was the introduction of MnDOT's Get Connected website, to help the public understand how Minnesota's transportation is funded. Check it out at www.dot.state.mn.us/getconnected/.
To learn more about MnDOT’s Wildly Important Goal – Enhancing Financial Effectiveness, visit the WIG website: http://ihub.dot.state.mn.us/efe/ and under Strategic Focus Areas, you'll find the latest battle updates. If you have general questions email them to WIG.DOT@state.mn.us. |
 |
|
|
|
|
 |
TABLE of CONTENTS
 |
MnDOT hosts Rise Above traveling exhibit |
By Mary McFarland Brooks
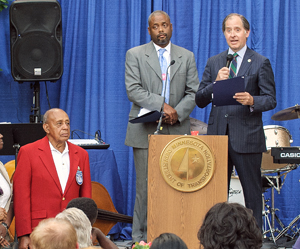
From left, Dr. Harold Brown and Department of Human Rights Commissioner Kevin Lindsey listen as MnDOT Commissioner Charlie Zelle reads a proclamation issued by Gov. Mark Dayton declaring July 16, 2014 as Minnesota Tuskegee Airman Day. Dr. Brown is a retired Lt. Col. in the U.S. Air Force and Tuskegee pilot. Photo by David Gonzalez |
To commemorate the 50th Anniversary of the Civil Rights Act of 1964, MnDOT, through the efforts of the African American employee resource group and the Office of Aeronautics, hosted the Rise Above traveling exhibit July 14-16 on John Ireland Boulevard. The exhibit, created by the Commemorative Red Tail Squadron, includes a film documenting the African American pilots who trained at Tuskegee Institute and flew in WWII, racking up reconnaissance and recovery records and executing incredible acts of bravery.
Ironically, after putting themselves in harm’s way, these same solders returned to a country where they were denied employment, housing and basic human rights. Despite these incredible odds, the 996 African American pilots and more than 10,000 ground crew, who also trained at Tuskegee Institute, went on to fill leadership positions in the military, as commercial pilots and in education and politics. The Rise Above exhibit also includes photos, quotes and timelines of the Tuskegee Airmen’s careers and features some of the remaining living pilots.
The film also documents the efforts of Don Hinz, who led the restoration of one of the P-51 Mustang planes that many of the Tuskegee airmen flew. To identify their 99th fighter squadron, the tails of their planes were painted red and they eventually became known as the “Red Tails.” The bomber crews, who the airmen protected, called them the “Red Tail Angels” and requested them as escorts. The German soldiers called them the “Black Birdmen.” According to the film, a WWII German soldier said, “When we saw the Red Tails flying over Berlin, we knew the jig was up.”
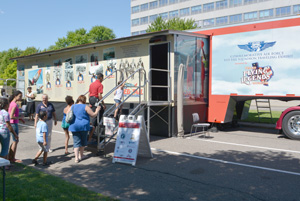
The African American employee resource group and the Office of Aeronautics hosted the Rise Above traveling exhibit July 14-16 on John Ireland Boulevard. Photo by Sue Roe |
More than 825 people saw the film during the three-day run and the audiences included state employees, school and youth groups and the general public. Retired Lt. Col., U.S. Air Force and Tuskegee pilot, Dr. Harold H. Brown and his wife, Marsha Bordner, were guests of honor at the event. They answered questions about the Rise Above film and provided interviews for local media outlets.
Dr. Brown was also honored at a reception on the plaza of the Transportation Building at the State Capitol. Commissioner Charlie Zelle read a proclamation issued by Gov. Mark Dayton declaring July 16, 2014 as Minnesota Tuskegee Airman Day. Seven other Minnesota Tuskegee Airmen combat pilots and service personnel and Dr. Brown were honored by the proclamation.
The evening included an introduction of Dr. Brown by Aeronautics Director Cassandra Isackson, who said that Col. Kenneth O. Wofford, a Tuskegee pilot, had served as director of MnDOT’s Aeronautics office from 1974 to 1984. More than 150 guests enjoyed hors d’oeuvres, and live jazz music by the Tommy Robinson Trio at the reception.
Several sponsors were involved in supporting the Rise Above reception including:
- The Minnesota Twins Ball Club
- The Minnesota Department of Human Rights
- The Minnesota Department of Transportation, Office of Aeronautics
- The Minnesota Association of Professional Employees
- The Minnesota Black Chamber of Commerce
- The Governor’s Council on Black Minnesotans
- Ravi Norman, CEO, THOR Construction
“MnDOT Aeronautics is happy and proud to have played a role in bringing the important story of the Tuskegee Airmen to the Capital grounds,” said Isackson. “The three-day Rise Above event was inspirational, educational and demonstrated the agency’s commitment to honoring local and national transportation heroes.” |
 |
|
|
 |
TABLE of CONTENTS
 |
Rumble strips are compared to mumble strips |
By Shannon Fiecke, Research Services & Library
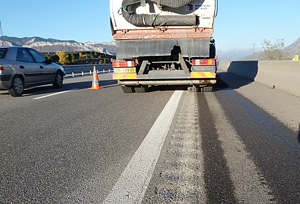
A Sinusoidal-style rumble strip, which provides less external noise, is ground into the pavement. Photo courtesy of the Wirtgen Group |
MnDOT is looking for a solution to noisy highway rumble strips and a European-developed product may provide the answer.
More and more counties are facing pushback on traditional rumble strips, which warn drivers they are getting too close to the centerline or road edge, but also produce stray noise that annoys people who live near the road.
“There is a strong concern statewide that these noise complaints will raise enough concern that legislation may be passed reducing their use,” said Ken Johnson, technical liaison in the Office of Traffic, Safety and Technology.
These concerns have led transportation officials to look at the sinusoidal (a.k.a mumble strip) design, which produces less external noise, while still alerting drivers.
Two research projects, one led by MnDOT and the other by the Minnesota Local Road Research Board, are evaluating the effectiveness of the sinusoidal rumble strip and whether or not it provides enough of a safety benefit to warrant a switch in populated areas. The sinusoidal rumble has a wave pattern ground into the pavement, while the traditional rumble strip doesn’t follow a wave pattern.
A research project in Thief River Falls, funded by the LRRB, is comparing both styles of rumble strips (see video).
The Office of Traffic, Safety and Technology plans to test different designs of sinusoidal rumble strips to find the one with the highest level of interior vehicle noise and lowest level of exterior vehicle noise.
If sinusoidal rumble strips are deemed effective, the chosen design will be used for centerlines and road shoulders in noise-sensitive areas throughout the state highway system.
Most complaints to counties regard shoulder rumble strips since narrow county road shoulders cause many drivers to hit the rumble strip. Meanwhile, most of MnDOT’s recent complaints are for its centerline rumbles, which are required on all rural, high-speed undivided roads in Minnesota, Johnson said.
MnDOT has considered allowing more exceptions due to residential noise concerns. However, doing so could result in more fatal and serious crashes. Sinusoidal rumbles are seen as a possible better alternative for these noise-sensitive areas.
|
 |
|
|
 |
TABLE of CONTENTS
 |
Noxious weed guide separates the good from the bad
|
By Sue Roe
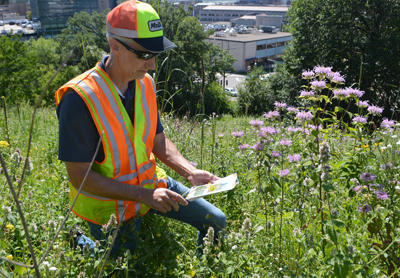
David Hanson, vegetation management specialist in the Office of Environmental Stewardship, uses MnDOT’s noxious weed guide to identify a plant on a scenic overlook. The guide helps MnDOT crews know how to identify and manage plants along roadsides, rest areas and other MnDOT-owned land. Photo by Sue Roe |
Anyone traveling around the state this time of year can enjoy the beautiful display of wildflowers and plants along the roadsides. In some areas, there are masses of vibrantly colored plants with appealing names such as Grecian foxglove, purple loosestrife, wild parsnip, dalmatian toadflax, and common tansy.
To the untrained eye, these plants beautify the roadsides and are considered “good” plants. To the trained eyes of MnDOT roadside vegetation crews, they are noxious and invasive, and can choke and overtake native plants that are less invasive and just as showy. Often these “bad” plants are harmful to people and animals because of their toxins.
One of the resources the maintenance crews use to identify the bad plants is the Minnesota Noxious Weeds guide. The guide was recently updated when the Department of Agriculture finalized the 2014 state noxious weed listings.
The guide has been available online since early 2012. It’s also available in printed “flipbook” form.
“Maintenance employees dealing with vegetation like the small book because it can be carried in vehicles to assist with plant identification,” said David Hanson, vegetation management specialist in the Office of Environmental Stewardship. Hanson researched, wrote and compiled the book and took most of the photos.
The guide categorizes plants on the Department of Agriculture’s noxious weed list. The four categories help MnDOT crews know how to manage the plant. For example, for plants listed on the eradicate list, the focus is early detection and rapid response to destroy above and below ground parts. Plants on the control list may be controlled with biological controls, herbicides or mechanical means such as mowing.
A unique feature of the guide is inclusion of comparison plants, both native and non-native, non-invasive species that are often confused for the listed invasive species.
Plants of all types are controlled along roadsides for safety reasons, including to maintain sight distances for crossing and merging traffic, to allow motorists to see approaching wildlife and to allow people to exit the vehicle if needed. Roadside vegetation control also aids in the identification of erosion issues and provides habitat and scenic qualities.
Hanson said the Minnesota Department of Natural Resources purchased copies for its field staff.
“We receive requests on a fairly regular basis wondering if this book is available in print form for distribution,” Hanson said.
Although a print version is not available to the general public, the online guidebook is accessible via home computers and smart phones for homeowners and people who like to hike and walk in state parks and trails.
For more information, go to MnDOT’s roadside vegetation management program website.
|
 |
|
|
 |
TABLE of CONTENTS
 |
Innovative sump retrofit provides savings, maintenance efficiencies while improving worker safety |
By Laurie Ryan, Customer Relations
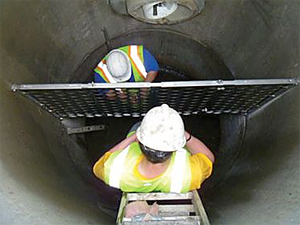
The St. Anthony Falls Laboratory Baffle helps keep sediment and pollutants out of lakes and streams. Photo courtesy of St. Anthony Falls Laboratory |
Following research and testing at the University of Minnesota’s St. Anthony Falls Laboratory the new SAFL Baffle will improve the efficiency of storm water sumps in removing sediment. The sump retrofit is designed to boost the performance of sump manholes for cleaning storm water runoff and will result in savings in equipment and maintenance costs, according to Beth Neuendorf, Metro District water resources engineer.
“Installing SAFL Baffles into storm sewer sumps will save taxpayer dollars, while also cleaning storm water runoff, meeting regulatory requirements and helping to keep our lakes, rivers and wetlands clean,” Neuendorf said
Before the SAFL Baffle was invented, standard sumps were unable to prevent captured sediments from washing out under high flow rates. Existing proprietary devices available for these purposes cost about $35,000 each. Retrofitted manhole sumps with the SAFL Baffle can perform the same function at an average cost of just $3,500each. The SAFL Baffle also makes maintenance safer and easier with no confined space entry.
The research was funded by MnDOT and the Local Road Research Board and initial development began in 2008. By 2011, the SAFL Baffle had been installed in more than 50 sumps by MnDOT, Minnesota cities and counties, and private entities. Installation of the new sumps has continued since 2011 with the technology proving to be both high performing and cost- and time-efficient.
The SAFL Baffle is a stainless steel sheet with holes in it, bolted vertically into a standard sump structure. The baffle slows the water down and allows the sediment to fall out of suspension and be captured in the sump. It also prevents the sediment from becoming re-suspended under high flows that would otherwise wash the collected sediment out of the sumps. MnDOT crews then periodically remove the sediment, so the sumps continue to capture sediment.
“Many lakes and streams in Minnesota are listed as impaired,” said Barb Loida, Metro District MS4 engineer. “This means they are not meeting Minnesota’s water quality standards. MnDOT is required to do its part in capturing pollutants to help improve water quality. The SAFL Baffle is a means for us to help do our part in a more cost-effective and efficient manner.” |
 |
|
|
 |
TABLE of CONTENTS
 |
Minnesota Freight Advisory Committee discusses legislative changes during panel discussion |
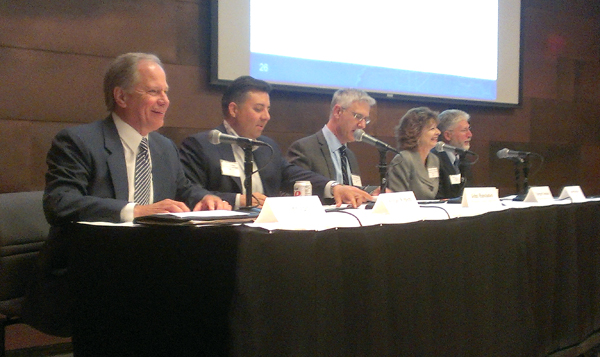
The growing economy’s increased freight shipments and legislative changes at the state and national levels dominated last month’s panel discussion of the Minnesota Freight Advisory Committee. MnDOT co-sponsored the event. Public, private and academic professionals attended the event at the University of Minnesota in Minneapolis. The panel of executives were, from left, John Apitz, Minnesota Regional Railroad Association; Michael Wilhelmi, Aggregate and Ready Mix Association of Minnesota; John Hausladen, Minnesota Trucking Association; Margaret Donahoe, Minnesota Transportation Alliance; and Scott Peterson, MnDOT director of Government Affairs, who moderated the panel. Photo by Greg Ruhland |
|
 |
|
|
 |
TABLE of CONTENTS
 |
On the Job: Barb Eastvold ensures that District 6 signs are correct |
By Mike Dougherty, District 6 public affairs coordinator
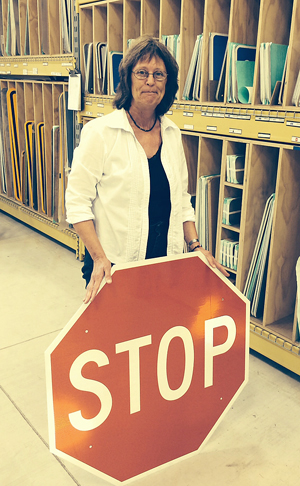
Barb Eastvold is responsible for all the signing programs in District 6. Photo by Mike Dougherty |
Work in the traffic office in Rochester is often about laws, regulations, distances, heights, populations and speeds.
So it’s funny to hear Barb Eastvold’s favorite part about her job: people.
But listen to her talk and you begin to understand the importance and value of the person who helps interpret, evaluate and understand all those rules and numbers. They all affect the safety of the motorists and pedestrians and it helps to have someone who enjoys that part of public service.
Eastvold is the transportation specialist who is responsible for all the signing programs in District 6 in Rochester. She’s been with MnDOT since 2001 and in the traffic office since 2007. She’s in charge of approximately 50,000 signs in District 6, which spans southeast Minnesota from Lonsdale to the Iowa border south of Brownsville.
Can you explain what your job entails?
I like helping people and making sure a motorist’s commute is a safe one. This is a very rewarding part of my job. There are basically three types of signs: Regulatory, Warning and Guide signs. Signs notifying road users of regulations (Stop, Right Lane Must Turn Right, or Speed Limit 55, etc.) are signs that are enforceable laws for which you can be ticketed. The warning signs (curve, stop ahead, RR crossing, etc.) do exactly that, warn. And lastly, guidance signs (Airport to the right, North US 52 right, Exit).
I prepare work orders to install or remove signs as needed. One example is when I receive a call from a school about a need for a “School Bus Stop Ahead” sign. I need to review the roadway for the proper spacing between existing signs before I can install the new sign. At the same time I need to remove a School Bus Stop Ahead sign when there is no longer a stop there so a driver isn’t being misled.
Another aspect of my job is handling requests for the Specific Service Signing Program. These are the blue and white signs located in rural areas on conventional highways and expressways. They are intended for restaurants, rural agricultural or tourist-oriented businesses, places of worship, gas stations, resorts and camping facilities. People will request a sign and I will go over the criteria necessary to see if they are eligible. If they qualify, and if there is room on the roadway to install the sign, the facility fills out an application and submits a fee of $854 per sign.
What’s the hardest part about the job?
The hardest part of my job is saying no to a sign request. A facility requesting a sign may not meet the minimum requirement of number of days in a week or hours in a day that they are open. It would be a great disservice to a motorist to turn a roadway only to find out a facility is closed. Often times a facility is eligible, but we do not have enough space on the roadway to place another sign. We need to meet the minimum spacing requirements shown in our Traffic Engineering Manual. If we cannot accommodate a requester, I try to suggest other options to them such as a billboard or a website.
How does your job in Traffic relate to other units in the district?
Working with other units within MnDOT is an integral part of my job. Recently, a citizen talked to John Paulson from our D6 Right of Way unit about their concern over noise from trucks using their brakes as they came into town. John asked me what the rules and regulations were for getting a “Vehicle Noise Laws Enforced” sign installed and then related this information back to the individual. I often receive questions from our Permits and Planning Units. I call on Rick Sunstrom and Heather Lott in the Central Office for answers to questions.
People don’t always realize how large some traffic signs are, do they?
No they don’t. The speed and type of roadway dictates the size of a sign and also the font used for the legend on the sign. For instance, Hwy 52 is a four-lane divided highway and the speed limit is 65 mph. The speed limit signs are 36 inches wide by 48 inches tall, while Hwy 30 is just a two-lane roadway with a speed limit of 55 mph, so those speed limit signs are 30 inches x 36 inches. The font size can range from a letter height of 6 inches to as high as 20 inches. The faster you are traveling the larger the size of the font and sign.
Is there a schedule to replace signs?
We are required to meet certain retroreflectivity requirements with the material we use on our sign panels. The life expectancy of the material is approximately 12-15 years and then we replace the sign. The material fades out from the sun and other natural elements. The material being produced today is much more reflective than it used to be, so we are getting a longer life out of our signs now.
What are some other trends?
I have been getting more calls for wineries wanting Specific Service Signs. They do qualify as rural agricultural businesses. It reflects the changes we’re seeing in agriculture in Minnesota. Rural wineries signal economic growth and it’s been interesting to see the number grow in our region.
What’s important in your job?
You have to be open to change! Just when you thought you knew it inside and out, the laws change. It is a never-ending learning process. It is always good to ask questions and look at things from all angles.
What did you do before you came to MnDOT?
I worked for the Fillmore County Highway Department in Preston. My duties there were to draw up grading plans and then when they were let, I went out in the field and was the inspector on the project. It showed me what I had had done wrong in the designing stage. I remember once not getting a ditch grade right and it ended up creating a small pond. The contractor put a lathe out in it with pink paint and the words, “LAKE BARB.” I never made that mistake again! |
 |
|
|
 |
TABLE of CONTENTS
 |
Staff resurrect District 1 gardens, share fruits (and vegetables) of their labor |
By Beth Petrowske, District 1 Public Affairs
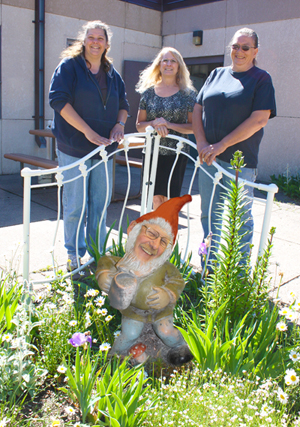
Near the white-themed garden are, from left,Toni Mattson, Barb Nelson and Barb Willett. In front is the D1 garden gnome, with the face of Dave Ollila digitally added. Photo by Beth Petrowske |
District 1 headquarters in Virginia has a large, enclosed courtyard located toward the center of the building. Brick walls surround the courtyard’s concrete floor, which has several openings designed for plantings. Considering northeastern Minnesota’s short growing season, this protected garden area is about as good as it gets.
Lisa Squires, a former District 1 employee, planted and cared for the courtyard gardens until she retired several years ago. No one had time to take on the gardening duties, and things got pretty ugly.
Then, three years ago, Barb Willett and Toni Mattson, general maintenance workers, and Barb Nelson, office and administrative specialist intermediate, took on the challenge with a goal of making the space beautiful and productive again.
The trio developed a plan for each of the seven gardens. Some, for example, are color-themed, another grows herbs and a third garden serves as a memorial for Anthony Lanier, a District 1 maintenance employee who died in 2012.
The transformation began by removing dead trees, weeding, working the soil and planting perennials and herbs that the women either bought or transplanted from their own gardens. Soon other employees began donating plants.
Now, after three growing seasons, the flower gardens are blooming with lilies, cone flowers, daisies and irises. The herb gardens are producing parsley, basil, chives, lemon balm, among other plants. And the vegetable gardens are lush with tomatoes, cucumbers, green beans and rhubarb. Willett and Mattson put the harvested vegetables and herbs in the lunchroom for all to share.
“We usually cut some of the flowers and put them in the lunchroom ─ so we always have fresh flowers,” said Mattson.
The once-neglected courtyard is now being used throughout the summer for retirements, birthdays, barbeques and brown bag lunches.
There is still much work to do. Willett and Mattson serve as lead gardeners as part of their maintenance responsibilities. However, other employees are beginning to use some of their break time to help with the gardening chores, and the gardeners welcome more help.
One garden features a huge horseradish plant. Willet digs out a section of the root in late summer, grinds it and brings it in to share, which doesn’t last long, she said.
“It’s great to hear the compliments from people coming out and saying this looks really nice ─ it makes me feel good,” said Willett.
One day while working on the garden plan Mattson suggested getting a garden gnome. Fleet Superintendent Dave Ollila happened to be standing nearby.
“Dave,” said Mattson, “Why don’t you be our garden gnome?”
Everyone laughed, including Ollila, who has become the butt of many jokes about being District 1’s official garden gnome.
Note: If you have any plants, seeds or garden ornaments that you would like to donate to the district, contact Willett or Mattson. |
 |
|
|
|