|
|
|
 |
TABLE of CONTENTS
 |
New technologies tested to monitor bridge scour |
By Nick Busse, Research Services
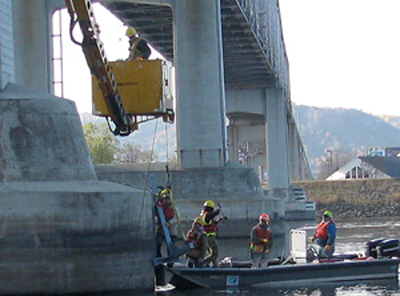
Workers install an active sonar system on the Hwy 43 Bridge over the Mississippi River in Winona. Photo courtesy MnDOT Bridge Office
|
A research implementation project could provide MnDOT with a new set of tools to help combat a major source of bridge failure.
The Bridge Office is testing several new methods of monitoring bridge scour — erosion that occurs around bridge piers and abutments during high water-flow events like floods. Acting Waterway Engineer Nicole Danielson-Bartelt said the project’s goal is to be able to monitor scour-critical bridges remotely rather than by sending maintenance staff on the water during difficult or hazardous conditions.
“There are a number of bridges that are pretty difficult to monitor, especially during high water events,” she said. “Typically, you need to get out on a boat and do either sonar readings or drop weights. It’s dangerous work to be out on the water during those types of events unless you have the right training.”
The project will evaluate several different monitoring technologies, including continuous monitoring equipment like tilt meters and active sonar. The sonar systems, which allow continuous stream bed and water surface elevation data to be transmitted to a website for graphical display, could provide benefits that go beyond monitoring individual bridges.
“The ability to collect continuous, long-term data could help engineers understand short term scour-fill and long term aggradation-degradation cycles,” said Solomon Woldeamlak, Bridge Office hydraulic engineer. He added that the data can be used as a calibration to existing methods of estimating scour at bridges.
Other devices being tested include “float-out” devices, which are buried in the sand around the abutment and send out a signal only if washed to the surface by a scour. Danielson-Bartelt said these non-continuous monitoring devices might be appropriate for bridges where installing permanent sonar is not advisable due to the presence of debris that could damage the equipment.
Monitoring equipment has been installed at two locations: the Hwy 43 Winona Bridge over the Mississippi River and the Hwy 14 Mankato Bridge over the Minnesota River. A final report on the project is expected in late 2014 to early 2015. Learn more about some of the products that are being tested on the website of ETI Instrument Systems, Inc., which provided the equipment.
|
 |
|
|
 |
TABLE of CONTENTS
 |
Modal Planning and Program Management Division undergoes changes |
By Rich Kemp
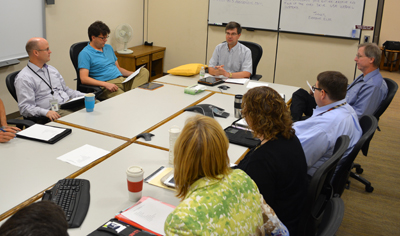
Mark Gieseke (top center) leads a staff meeting for the Transportation System Management Office. Photo by Rich Kemp |
Adding to the department-wide organizational changes previously announced is the news that the Modal Planning and Program Management Division has reorganized from seven offices down to five. The Capital Programs and Performance Measurement Office, Statewide Multimodal Planning Office and the Transportation Data and Analysis Office have combined to form the Transportation System Management Office under the leadership of Mark Gieseke. The Research Services and Library section, part of the former Policy Analysis, Research and Innovation office, is also part of the new Transportation System Management office.
Four other offices – Transit, led by Mike Schadauer; Freight and Commercial Vehicle Operations, led by Bill Gardner; Aeronautics, headed by Cassandra Isackson; and Passenger Rail, led by Dan Krom – are also part of the division.
Gieseke directed the Office of Capital Programs and Performance Measurement and has been employed at MnDOT since 1983.
“We are hoping that being together in one office will help us work together to achieve key agency goals,” said Gieseke.
The TSM office will manage the overall strategic program management of the transportation system to include operations planning, performance-based planning, asset management, research and library services, data and information management, and risk management.
In the new structure, Mark Nelson will manage transportation planning, data and analysis; Brian Gage will be in charge of performance measures and program management; and Linda Taylor will manage research and library services.
“These organization changes ensure that the Modal Planning and Program Management Division is poised to advance the agency’s financial effectiveness through high-quality resource management and integrated transportation planning and programming,” said Tim Henkel, division director.
Among many projects the TSM office oversees are: the growing research program, the transportation information system, MAP-21 implementation, the Corridors and Commerce program and the 20-Year Minnesota State Highway Investment Plan. |
 |
|
|
 |
TABLE of CONTENTS
 |
MnMAP provides web-based tool for sharing, editing GIS data |
By TK Kramascz
To promote transparency and foster data sharing, AASHTO’s Technology Implementation Group, along with MnDOT, Pennsylvania and North Carolina, are working to increase GIS data usage for internal and external partners.
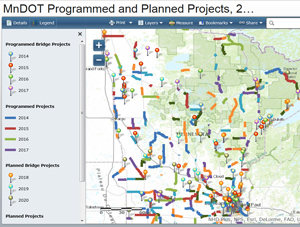
A map of MnDOT programmed and planned projects that was created with the new MnMAP program. |
Termed UPlan, the effort provides a powerful yet easy way to use web-based decision-support mapping. It’s an informational tool for completing complex planning and project development tasks. UPlan allows complete or selective data sharing among various work units within state DOTs and also allows selective data sharing between state agencies, other DOTs, and the public.
MnDOT’s effort, called MnMAP, allows users to see their data on a map and gives them the ability to share and edit that data with others. It was developed using ArcGIS Online.
"By compiling GIS data that is organized and focused, MnDOT and stakeholders can establish more positive and productive working relationships, understand issues and reduce effort and duplication," said Jesse Pearson, project manager. "This leads to reductions in costs and time requirements, thereby helping to manage successful projects with fewer impacts."
Currently MnMAP shows users the national highway system, MnDOT's 2013 construction projects, programmed and planned projects from 2014 to 2023, and a 2030 transitways overview. Future offerings likely will include story maps that depict high-profile construction projects, a pavement quality map and a functional class map,
ArcGIS Online is a collaborative, cloud-based platform that lets employees or other members of an organization create, share, and access maps, applications and data, including authoritative base maps published by ESRI or Bing.
Visit MnMap and see what the buzz is about. |
 |
|
|
 |
TABLE of CONTENTS
 |
HR Summit emphasizes “carpooling” skills to create networks across locations, disciplines |
By Rich Kemp
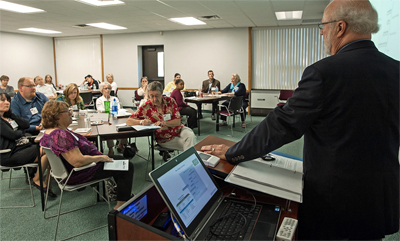
Dr. Fred Kiel presents some of his research findings regarding the impact of moral intelligence on organizations to HR Summit attendees during the event Oct. 1 at the Arden Hills Training Center. Photo by David Gonzalez |
Carpooling skills for the future was the theme of the fifth annual HR Summit Oct. 1 at the Arden Hills Training Center. More than 100 MnDOT employees from human resources and training, representing all of the districts and CO, attended the one-day training session.
Karin van Dyck, Human Resources director, asked the attendees to think about a carpool as an analogy for going on the same journey: changing drivers when needed, sharing the work, and arriving at the same destination.
“Think of this definition of a carpool as it applies to networking and collaboration amongst the HR and Training fields,” said van Dyck. “Our goal is to work on ‘carpooling’ our ideas, our strategies, our successes and challenges. The goal is to see how we can create networks across locations and disciplines.”
Van Dyck told participants to promote effective networking in their workplace and demonstrate it in their day-to-day behaviors.
“We hope each individual, each work group or office, and each district can foster such behaviors,” she said.
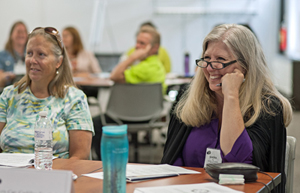
Susan Ronchak, Human Resources, and Sandra Rike, Metro District, attended the HR Summit at the Arden Hills Training Center Oct. 1. Photo by David Gonzalez |
The keynote speaker was Jack Mateffy, who has helped large and small public and private sector clients to boost employee performance and engagement. Mateffy asked the group if they were satisfied with their job. His goal during his presentation was to help them discover what drives them to work today.
The employees were divided into groups, called carpools. In keeping with the theme, the groups were called muscle car, sports car and luxury car carpools. They rotated between presenters to discuss how people must possess a high degree of interpersonal communication skills, how the moral habits of leaders affect organizational dynamics and, ultimately, organizational outcomes, and to learn the foundations of human resources management philosophy.
Commissioner Charlie Zelle spoke to the group about MnDOT’s information and outreach program called Minnesota GO. He also talked about getting the people of Minnesota to express their favorite “A to B destination” and to understand the importance of transportation in Minnesotans’ daily lives. Zelle encouraged the employees to share the message with friends, families and social groups.
The summit closed with a few words from Sue Stein, Corporate Services Division director. For more on the summit, check out the HR Summit website. |
 |
|
|
 |
TABLE of CONTENTS
 |
Tools on the web |
By Libby Schultz
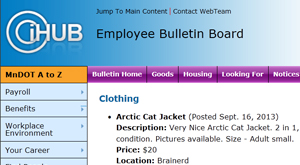
Example of a posting on the Employee Bulletin Board. |
Editor's Note: “Tools on the web” is
a new feature of Newsline that highlights useful tools on iHUB.
Employee bulletin board
Trying to get rid of that old couch, sell some season tickets last minute, or want to find out when your co-worker’s retirement party is? The Employee Bulletin Board on iHUB might be a good place to start.
MnDOT employees can use the bulletin board to post items they want to sell or give away, notices about retirements or funeral services, and inquiries for wanted items.
The Employee Bulletin Board started seven years ago after the Central Office building rehabilitation eliminated the physical bulletin boards in the building.
“There used to be bulletin boards all over the building, filled with fliers from people looking to sell their stuff,” said Lucy Kender, Human Resources, who also maintains the site.
Enough employees were interested in having something like the old bulletin boards, she said, so an online version was created.
“[The bulletin board] is trying to use technology to replace an old-fashioned way of doing this,” said Kender. “At the same time, it’s helping employees connect to sell their goods.”
While created to fulfill a need at Central Office, the Employee Bulletin Board now connects employees in all the districts. Some popular items on the bulletin board include tickets to events, vehicles, furniture and kids’ clothing.
“The bulletin board is all about employees having an opportunity to sell goods to a wider audience in a more organized way,” said Kender.
Almost anything can be added to the bulletin board, but here are some guidelines:
- No items or advertisements for a personal business
- No links to other ads (e.g., craigslist.com)
- No photos
Items will be left on the bulletin board for one month, or until the item sells, whichever comes first. The bulletin board is updated daily and receives up to 10 submissions every week, so be sure to check back regularly.
Check out the employee bulletin board at http://ihub.dot.state.mn.us/bulletinboard/. |
 |
|
|
 |
TABLE of CONTENTS
 |
Airport professionals statewide share expertise at annual AirTAP forum |
By Dan McDowell, Office of Aeronautics
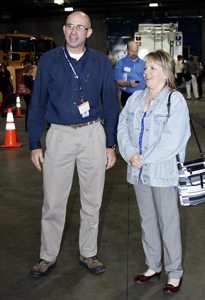
Cassandra Isackson, Aeronautics director, discusses airport field maintenance vehicles with St. Cloud Airport Manager Bill Towle during the AirTAP conference. Photo by Dan McDowell
|
The 2013 Airport Technical Assistance Program Fall Forum, held Sept. 26-27 at the Metropolitan Airports Commission Facilities in the Twin Cities, brought together public- and private-sector airport professionals from across Minnesota to share expertise on such topics as minimum operating standards and all hazards planning and emergency preparedness.
The annual forum included behind-the-scenes tours of the Minneapolis-St. Paul International Airport and MAC facilities.
The forum was sponsored by MnDOT, the Center for Transportation Studies at the University of Minnesota and the Federal Aviation Administration.
For more information about AirTAP, see www.airtap.umn.edu/about/.
|
 |
|
|
 |
TABLE of CONTENTS
 |
On the Job: If it involves hazardous materials, Jim Fox might be on the scene |
By Greg Ruhland, Office of Freight & Commercial Vehicle Operations
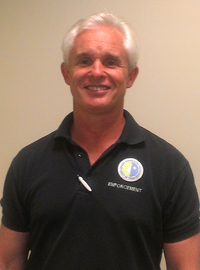
Jim Fox is a hazardous materials specialist. Photo by Greg Ruhland |
After joining MnDOT in 1990, Jim Fox became a hazardous materials specialist with commercial vehicle operations in June 1992—first at the South St. Paul location, now at Oakdale. Prior to this, he worked eight years in commercial vehicle enforcement for the Minnesota State Patrol.
Fox, along with Kevin Kampa, Randy Kudzia and Kory Wiech, provide on-call hazardous materials incident responses and conduct audits on regulated commercial freight shippers and transportation providers. This is to ensure that shippers are complying with safety and hazardous materials regulations.
What is the hazmat specialist’s role?
When a safety incident happens that involves chemicals or other hazardous materials, myself and the others help the incident commander as the “technical expert” for transportation issues. For example: take a cargo tank, a cylinder or a five-gallon drum. We know how each packaging works. We understand the process of transferring products from a damaged package to an intact package. And we know the equipment and methods that work best.
We are also the experts on recovery. For example, if a cargo tank is rolled on its side, we make sure that it is properly upright to avoid larger breaks or spills. We are also on scene to investigate the cause of an incident—were there regulation violations or a packaging failure?
Do you have a busy season?
Spring and fall are our busy seasons. Much of our responses are agricultural as farmers plant, harvest or haul refined petroleum fuels. Or, they are seasonal as propane is used for grain-drying and home heating, or chemicals are moved.
What happens when you can’t respond to every incident that arises?
We don’t... incidents are handled differently. Sometimes travel time is too great. Other incidents do not demand our expertise on scene; over-the-phone consulting with a carrier or shipper is enough.
What recent experience stands out to you?
This spring, a train collided with an anhydrous ammonia semi-trailer near Murdoch, Minn. It’s still an open investigation, but the rear of the trailer was in the path of an oncoming train. There was a significant release, the driver was killed, cleanup took five days and Hwy 12 was shut down for a long period of time. MnDOT maintenance and safety were involved and even other agencies, such as the Department of Agriculture, Homeland Security and the State Patrol.
Tell me more about your typical regulatory activities.
We work in cooperation with the Department of Public Safety to regulate hazmat incidents. We might do an audit or an investigation: What do records show for the hours of service? What are the compliance records for alcohol and controlled substance testing? What are the inspection records for cargo tank testing? Maybe a test or inspection wasn’t performed on time or at regular intervals. Problems like these can lead to hazmat incidents.
We also perform dock audits – hazmat packages from vendors like UPS leaving the shipping dock. Any violations during these audits could lead to our shipper “intervention.” The four of us are involved with these. We also conduct cargo tank facility reviews, ensuring that companies properly test and inspect cargo tanks. We conduct regular compliance reviews and soon will be doing new entrant audits.
How do you inform and educate customers (e.g., trucking companies) about their obligations?
I just finished teaching a two-day Hazardous Materials Transportation class. The four of us teach the class and it’s offered online. We’ll often schedule more specific classes. We assist companies with the details they need to take care of, and we go to industry functions—conferences with propane gas, petroleum and other associations in Minnesota.
What do you like best about your job?
No day is the same. One of the four of us is always on call 24 hours a day, 7 days a week. Sometimes we have to travel long distances in a short period of time, so we use our lights and sirens—whatever the emergency dictates.
|
 |
|
|
|