|
|
|
 |
TABLE of CONTENTS
 |
Maintenance “tools of the trade” demonstrated at Sandstone Truck Station |
By Beth Petrowske
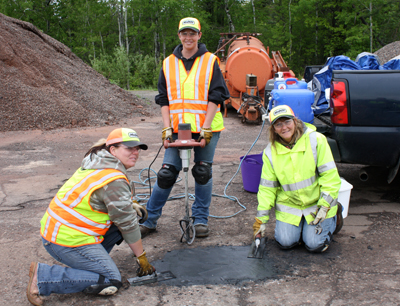
From left, Dawnelle Berghult, transportation associate, Tanya Maki, transportation generalist, and Jill Besch, transportation generalist, finish a patch using RapidPatch. The formula for this patch is comprised of water, RapidPatch Pavement Repair Activator and taconite tailings. A benefit of this patching process is that it can be mixed in small batches. Photo by Beth Petrowske
|
Maintenance employees from all over Minnesota attended a large-scale paving demonstration June 6 at the Sandstone Truck Station.
Greg Pierzina, District 1/Duluth maintenance superintendent, coordinated the event, which was attended by more than 150 maintenance professionals.
"There are many challenges ahead of us to reach our pavement preservation goals," said Pierzina. "This event gave us an opportunity to see equipment from other districts being operated and will help us decide what would be good to add to our fleet."
The event started with a short presentation, which provided information about each of the 18 pieces of equipment on display at the event, its benefits, strengths and weaknesses. After the presentation, attendees had the opportunity to see all of the equipment in action.
The demonstration areas covered two large parking lots. Attendees wearing fluorescent-orange safety gear watched the demonstrations as the acrid smell of bituminous, diesel, hot oil and other pavement additives permeated the air. The demonstrations were repeated throughout the morning to give everyone an opportunity to see as much as possible.
Maintenance supervisors from all districts, and various county and city staff were invited to the event. Equipment vendors were not invited, to ensure that attendees could freely discuss their opinions about equipment.
According to MnDOT’s “Better Roads for a Better Minnesota” website, “State performance measures currently show that about 750 miles of trunk highway in Minnesota are classified as “poor” condition. Without additional investment, the number of miles in “poor” condition is estimated to increase to 1,900 by the year 2020.”
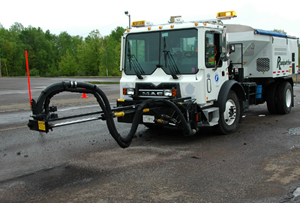
A maintenance crew from District 4 demonstrated an air patcher during the paving demonstration June 6 at the Sandstone Truck Station. The new patching system is stationed at the Alexandria Truck Station. Photo by Rich Kemp
|
Steve Lund, state Maintenance engineer, spoke at the event and is optimistic about the future.
“This is an exciting time to be in Maintenance at MnDOT,” said Lund. “Mike Barnes, our operations director, is pro-maintenance and wants our maintenance efforts to be effective and efficient.”
Barnes has developed and secured funding for a new program called “Better Patching for Better Roads.” The aim of this program is to improve MnDOT pavement maintenance techniques and products. Among other things, the program will focus on improved patching technology and longer lasting patches.
"This event offered even veteran maintenance professionals an opportunity to see equipment demonstrated that they may have never been able to see operated before,” said Duane Hill, District 1/Duluth engineer. “The information learned during this half-day event should have long-lasting benefits in pavement management throughout the state.”
For more information about the equipment, check out the Powerpoint presentation or contact Greg Pierzina at gregory.pierzina@state.mn.us or 218-742-1082. |
 |
|
|
 |
TABLE of CONTENTS
 |
Construction of Interstate 90 crossing off to good start |
By Kristin Kammueller
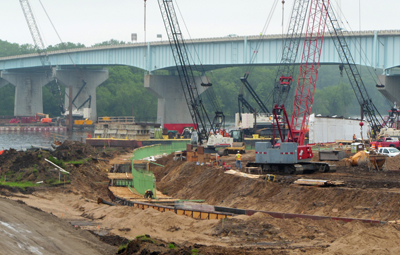
Construction crews begin work on the new I-90 crossing between Dresbach, Minn., and La Crosse, Wis. Photo by Eric Breitsprecher.
|
The Interstate 90 Bridge spans the Mississippi River between Dresbach, Minn., and La Crosse, Wis. Built in 1967, the 2,490-foot steel girder, fracture-critical bridge carries four lanes of traffic and has narrow shoulders.
Construction of a new crossing began in January when parts of the Dresbach Travel Information Center closed to allow crews to stockpile materials for the project. Since then, access to the U.S. Fish and Wildlife boat launch from the TIC closed, the Mississippi River Bike Trail between La Crescent and Dresbach closed and I-90 traffic is reduced to one lane on both the Wisconsin and Minnesota sides of the bridge.
Crews are currently working on the new retaining walls near the TIC, excavation for one of the piers and constructing dock walls for the barges to stop at when dropping off supplies.
The new crossing will consist of two separate bridges parallel and upstream from the existing bridge. It will include 12-foot outside shoulders and six-foot inside shoulders, as well as an eastbound acceleration lane, greatly improving safety. The new bridges will also have a 100-year design life.
“Despite the weather, I’m happy with the progress that is being made,” said Mark Anderson, project manager. “Once we get the crossovers built, and all traffic is moved to the westbound lanes, work can begin on the grading in preparation for the new interchange.”
In addition to constructing a new I-90 river crossing, this project also includes reconstructing the Hwy 61/Hwy14 and I-90 interchange.
The new interchange configuration will provide full movement with no signals between I-90 and Hwy 61. The heavily used westbound I-90 to southbound Highway 61 will feature a fly-under ramp allowing continuous movement with no competing traffic.
The $187.5 million project is a cooperative effort between the Minnesota and Wisconsin departments of transportation and is expected to continue into 2017.
For more information about the Dresbach Bridge project, visit www.mndot.gov/d6/projects/dresbachbridge. |
 |
|
|
 |
TABLE of CONTENTS
 |
Electronic purchase request system on the way |
By Susan Walto

An electronic purchase request system is coming to MnDOT in August. |
The purchase request system is about to become faster and easier. The Electronic Interoffice Requisitions system will be implemented in August. EIOR will replace MnDOT’s current paper-based requisition process. Once the program has been implemented, all requests must be made through EIOR.
In looking for an alternative to using the SWIFT eProcurement Requisition module, MnDOT chose to implement a proven system that was built with the state’s needs in mind.
“Implementing EIOR now will position MnDOT to implement the SWIFT module in the eventuality that the state mandates it,” said Bill Roen, TranSWIFT project director.
The EIOR application has been used successfully at the Department of Human Services for more than 10 years and the Department of Corrections for more than five years. EIOR is currently being modified to fit the agency’s processes that are unique.
Employees will find that EIOR is easy to learn and use. They can also quickly send a request to their supervisor or approver, who will be notified by email. Once approved, requests for purchases automatically are sent to the buyers for entry into SWIFT as purchase orders.
“Employees will be able to send their requests to approvers electronically and see the status in EIOR. The days of walking a paper request around for signature will be over,” said Craig Gardner, Materials Management director.
Reporting and tracking will also be easier with EIOR. Employees and buyers will be able to quickly pull up an EIOR by number to see who requested, approved and received an order. EIOR also supports the agency's ongoing efforts in safeguarding MnDOT and records management.
Training for requestors, approvers and buyers will be offered in July to get ready for the August implementation. Announcements and more information will be sent in June. For more information on EIOR, contact Craig Gardner at craig.gardner@state.mn.us or 651-366-3163. |
 |
|
|
 |
TABLE of CONTENTS
 |
More than 200 participants make Leadership Development Program’s first year a success |
By Kelly Charbonneau Of the 229 MnDOT employees participating in the first year of the department’s Leadership Development Program, 95 percent will receive a certificate of completion this summer, according to Carol Hennekens, LDP manager.
“These participants worked hard during the last year to meet self-established goals. They had the chance to participate in more than 30 Learning Opportunities, in addition to any independent work they identified themselves to help cultivate the skills of effective leadership,” she said. “The first year of the Leadership Development Program was a success.”
“The Leadership Development Program gave me the impetus to seek training to help prepare me for the inevitable challenges we face,” said Jim Aamot, information technology specialist. “My personal growth in strategic thinking and emotional intelligence has helped me to change my thinking in a beneficial way.”
Opportunities that the participants had during the year included getting a holistic understanding of the organization through touring various MnDOT facilities, and training in several aspects of leadership in classes such as Leadership Foundations, Effective Presentations, and Life Orientations Training. They also studied individually through job shadowing, cross-training and stretch assignments.
Michael Carli, Oversize/Overweight Permits Section, another 2012 program participant, applied his experience to all aspects of his life.
“While coaching I have learned three very important things: first, to communicate my goals and expectations; secondly, know a player’s strengths and use them to benefit the team; and third, when we play as a team and everyone puts forth the effort, we are successful. I don't necessarily associate success with wins and losses - it’s about improving,” Carli said.
The 2013-2014 Leadership Development Program begins Aug. 1. Enrollment will be accepted July 1- 19. To learn how to enroll and decide whether the program is right for you, visit the Leadership Development Program website.
|
 |
|
|
 |
TABLE of CONTENTS
 |
MnDOT, U of M develop portable weigh-in-motion system |
The MnDOT Research Services staff visited the MnROAD pavement research facility for a live demonstration of portable weigh-in-motion technology being developed by MnDOT and the University of Minnesota. You can learn more about the system on the MnDOT Research Services website.
|
|
 |
|
|
 |
TABLE of CONTENTS
 |
Eight ways Lync can improve your workload |
By Bob Filipczak
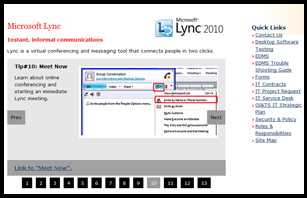
All MnDOT employees now have access to Lync. |
Lync rolled out to all MnDOT employees on June 13. In the last issue of Newsline, we covered most of the features of the program. However, can Lync actually help you decrease your workload?
Early results from the initial deployment of Lync should interest anyone who wants to work more efficiently.
- More than half of the early testers said they did less email—yes, less email—because they use Lync.
- More than 40 percent of users said they fielded fewer phone calls because of Lync.
- More than 10 percent of early adopters said they attended fewer Adobe Connect meetings, traveled less to meetings, and attended fewer meetings overall.
- More than half of employees testing Lync said they got faster responses to questions.
- Almost a third of the users reported that they collaborated more using Lync.
- Users also said they did more desktop sharing (no more guessing what we both are looking at), more virtual meetings (fewer missed meetings due to weather) and overall efficiency gains.
- One of the simplest features of Lync—knowing whether a coworker is available at their desk—has helped many early users have more effective face-to-face interactions.
- And for remote workers, an inexpensive webcam can get them face-to-face almost anywhere in the state in a few seconds.
Everything you need to know about Lync’s features can be found on iHub.
|
 |
|
|
|
|
 |
TABLE of CONTENTS
 |
On the job: Rob Holschbach helps oversized trucks find right route |
By Rich Kemp
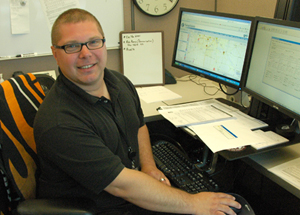
Reaching out to trucking companies to make sure that MnDOT grows with the pace of industry is important to Rob Holschbach, senior tech and the heavy haul project coordinator in the Oversize/Overweight Transportation Permit section. Photo by Rich Kemp |
Rob Holschbach takes his job in the Oversize/Overweight Transportation Permit section seriously. Holschbach was involved in the transportation industry for many years, before joining MnDOT in July 2007. He started working in the permit section of the Office of Freight and Commercial Vehicle Operations in April 2008.
OFCVO Permits has 10 permit techs who work with customer requests for oversize and overweight vehicle permits. Holschbach is one of three senior techs and the heavy haul project coordinator.
What does the OFCVO Permits do?
Our mission is to support the safe and efficient movement of oversize and overweight loads on Minnesota’s trunk highways.
When is a special permit required?
We issue all statewide permits for interstates, U.S. and Minnesota highways, not local roads. We issue transportation permits that allow movement of loads that exceed the legal dimensions and weight of 8 feet 6 inches wide, 13 feet 6 inches high, 75 feet long or over 80,000 pounds. Vehicles that exceed these limits must request a permit from us and receive approval to operate on our highways. We set the general conditions those loads operate under, such as date and time of travel, specific route, whether they need escorts, etc.
What is your typical day like?
We are very busy during the summer months. In 2012, we issued more than 91,000 permits. We review the information that is submitted on an application and make sure it is correct and complete. We check that the route is clear of construction or other constraints and that there are no bridge height deficiencies. Coordination is done with district offices and sometimes with the State Patrol and bordering states. We answer an average of 125 phone calls a day between the hours of 8:30 a.m. and 3 p.m.
What is required for the carriers to obtain oversize/overweight permits?
The majority of permit applications are requested through RouteBuilder, our online permitting system. We also accept applications by email, fax or walk-in to the permit counter on the first floor of the Central Office.
We have used the RouteBuilder system since 1990. The system cross-references various roadway characteristics and bridge ratings for height and weight restrictions, district information and construction information. It is complex—there is a lot of thought that goes into it. We’re not just rubber stamping a piece of paper and sending it out.
There are many checks and balances we review, and we rely heavily on our district offices when there are questions regarding specific road constraints.
What do you like about your job?
I really like the challenge. It is never the same day to day, interacting with individuals around the country. Helping the customer succeed is very rewarding. I feel like I have accomplished a significant task when I am able to help someone navigate large loads through our state safely.
What is your busiest time of the year?
When the spring road bans are lifted, it gets really busy in our office. Our busiest season is from May to October.
Was there any kind of impact in Minnesota from the Interstate 5 Bridge collapse in Washington State?
We haven’t seen the results of the investigation, but it makes you want to focus even harder. MnDOT is an industry leader; one that other states look to for process enhancements. I think all states are taking a closer look at the type of bridge that fell in Seattle. Although an over-height, permitted load is alleged to have caused the bridge to fall, it doesn’t appear that it was the fault of the permitting agency. OFCVO Permits has recently begun discussion with the MnDOT Bridge Office and Transportation Data and Analysis to see if we need to place over-height detection monitors on some of our more critical bridges, so we don’t have a situation like Seattle.
Do you work on any other projects?
I do outreach and networking with trucking companies. Things change fast in this industry—configuration and types of trailers. It is helpful for us to get out there and meet with customers and see some of the things that are happening, see what the upcoming challenges are. An example of this is our work with the Wind Energy Industry and working with General Electric project managers to identify highway corridors to safely route high volumes of wind tower components. I am also involved with our WINNDOT initiative that was established to create a seamless border between Minnesota and Wisconsin, and to help promote uniformity in permitting. Wind Energy has helped the states work together to solve problems and to coordinate routes between our borders.
We need to grow with the pace of industry and continue to keep our permits staff informed of new trends and continually changing regulations.
More information on permits for oversize and overweight vehicles can be found at: www.mndot.gov/cvo/oversizeDo you or a co-worker have an interesting job to share with readers? Click here to send us your ideas, and we’ll contact you for more information.
Recent employee profiles:
|
 |
|
|
|