By Stephany Osuji, Office of Customer Relations
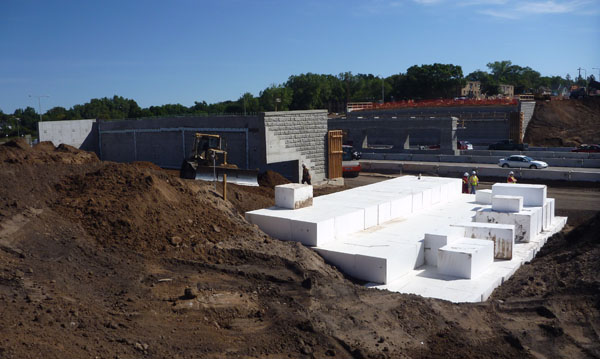
Crews install Geofoam west of the Maryland Avenue Bridge site in St. Paul to reduce potential long-term settlement problems. Photo by Derrick Dasenbrock |
The recent Interstate 35E Maryland Avenue bridge project in St. Paul is just one example of MnDOT’s commitment to innovation. Various innovative techniques, most notably the use of Self-Propelled Modular Transporters to move the main span into place, highlighted the project. However, a lesser-known innovation proved essential in providing stability beneath Maryland Avenue in areas where the local soil was unstable.
Expanded Polystyrene, often referred to as Geofoam, is a low-density Styrofoam commonly used as a lightweight fill on construction projects. The foam is approximately one percent the weight of normal fill, such as gravel or dirt, and is used where hard-to-remove organic soils would otherwise compress when being backfilled.
Geofoam has become the lightweight fill of choice for MnDOT’s Foundations Unit for several reasons, according to Rich Lamb, foundations design build engineer. It has similar strength characteristics to soil, but has the enormous benefit of being extremely light—1-2 pounds per cubic foot.
“Using Geofoam is a long-term solution to help stabilize roadways over compressible soils where it would be expensive and hard to remove the poor soils,” said Joey Lundquist, Metro District Design engineer.
During the Maryland Avenue Bridge project, Geofoam was placed under the pavement along Maryland Avenue and the ramps to reduce potential long-term settlement problems while protecting the existing utilities on Maryland Avenue, just west of the new bridge.
Construction crews installed the Geofoam by first excavating the area where the foam would be placed. The blocks were then installed in a staggered pattern until the foam reached the appropriate height. Once the geofoam was in place, it was covered with a thin plastic barrier called a geomembrane. The geomembrane protects the Geofoam from petroleum-based spills. Finally, the foam was backfilled with appropriate grading material and ready for concrete paving.
Although the upfront material cost is high at $50-$80 per cubic yard, Geofoam has proven to have a high return on investment. It also has a track record of being an effective material when dealing with embankments and poor soils, according to Lamb.
“With minimal excavations, we can now construct roadway embankments with Geofoam and basically have no load imparted on soft, organic soils,” Lamb said. “This means virtually no settlement and safe, smooth roadways.”
Another benefit of Geofoam is how quickly it can be installed, which saves on construction time. Each 4-by-8-by-3 foot block weighs 127 pounds and can easily be handled by four workers, according to Lamb. As much as 1,000 cubic yards can be placed each day.
“Without Geofoam on the Maryland Avenue Bridge project, the contractor would have had to perform very deep and costly excavations to remove the poor soils,” Lamb said. “This may have extended the construction time, something that was a great concern for such a high-profile project.” |