By Jessica Wiens
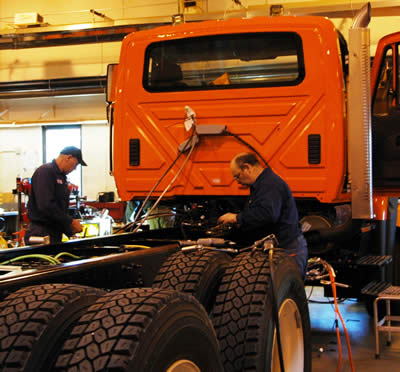
Randy Wobschall (left) and Randy Beck work on Phase 1 additions to this truck. Work is much easier to complete before the box is in place. Photo by Jessica Wiens
|
When winter weather hits, MnDOT plows are on the roads. But the process of getting new plows ready for use is a big task. Several employees at MnDOT’s Central Shop at Fort Snelling in St. Paul—including more than 10 heavy equipment mechanics—coordinate the effort for all districts across the state. MnDOT ordered 48 trucks in FY 2013 and 56 trucks in FY 2012.
The process begins in the spring and summer, when districts each decide what equipment to purchase with the upcoming fiscal year’s budget. On average, tandem—or double rear-axle—trucks cost $210,000 and single-axle trucks cost $170,000.
District shop supervisors/fleet managers then coordinate with Randy Cameron at Central Shop to order their trucks. In fact, Cameron goes through 11 pages of options for each truck to customize each cab and framework—known as the cab/chassis.
The local dealer works with a manufacturer, currently International, to build the cab and chassis in Texas. How quickly those get built greatly depends on the truck economy. According to Cameron, it could take anywhere from a few months to one to two years.
Cameron estimates that about 20,000 parts go into just the truck chassis.
“Assembling one of these truck chassis is like a car assembly line, except it’s much slower,” said Bob Ellingsworth, fleet manager. “The manufacturer may only assemble one or two trucks a day.”
In addition, the manufacturer punches anywhere from 70-90 extra holes into the truck frame so that MnDOT can add extra components, including the front plow, wing plow and underbody plow.
While MnDOT waits for the chassis to come in, Central Shop coordinates other parts of the truck, including the first aid kits, hydraulic hoses and fire extinguishers. Additional parts to customize the plow come from a partnership with MINNCOR Industries, a business through the Department of Corrections that employs prisoners.
Before the entire order arrives, the manufacturer sends one or two pilot trucks for MnDOT to inspect and ensure everything is correct for the larger order. Inspectors usually find small changes and tweaks for the full order.
After the full order begins, the manufacturer sends trucks to the dealer in Minnesota, who does an inspection and then sends them to MnDOT’s Central Shop. This is when the trucks get customized to become snowplows.
Work for MnDOT is split into two phases. Phase 1 includes installing the basic electrical system and removing the fuel tank, battery box and seats before installing other hardware and rerouting air and fuel lines. All Phase 1 work takes about 60 hours of labor per truck.
Then the truck goes back to a vendor, who installs the box, hoist and hydraulics system. That takes about 40-50 hours of labor per truck.
Phase 2 at MnDOT includes installing the sander, wing plow and MDSS system, finishing electrical work and adding lighting. This takes about 80 hours of labor per truck.
Once all of this is complete, districts send employees to pick up their truck. Heavy equipment mechanics in the districts also may do some work to further customize the truck for their district.
Steve Lund, state maintenance engineer, recognizes how difficult it can be for districts to wait more than a year for a truck.
“We are trying a few new methods to shorten the process and get more trucks to the districts faster,” Lund said. |