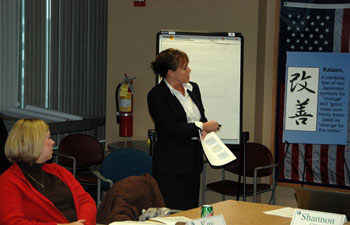
Kay McDonald, Office of Information & Technology Services, listens as Mary Prescott, Mn/DOT LEAN Program director, summarizes the Enterprise LEAN initiative. Photo by Nick Carpenter |
By Nick Carpenter
In Japanese, the word “Kaizen” means “change for the better.”
A team of Central Office employees recently completed a Kaizen training event aimed at helping the Office of Information &Technology Services “change for the better” by identifying areas for improvement in its current business process and designing a new, more efficient process that adds value at every step.
Through the course of the event, the team developed a significantly streamlined process that will reduce average IT project duration from 44 months to 26 months, according to John Rindal, IT Office. Several changes were made to the process to reduce project duration, including:
- Number of process stages—reduced from five to three.
- Project basis—all projects must be requested by or with the endorsement of a division director, office director or district engineer.
- Project selection—all projects are selected much earlier in process based on higher-level information and estimates.
- Decision making—one “go” or “no-go” decision point rather than multiple ones.
Division directors select Kaizen events that are a priority for the department. The events are put on as part of the Enterprise LEAN initiative—a coordinated state government program for improving the organizational performance and results in Minnesota’s state government agencies. LEAN’s main objective is to help state government work better for its customers and employees by using an approach that embraces the Six Sigma tools and total quality management philosophies, according to Mary Prescott, Mn/DOT LEAN Program director and department representative on the statewide steering committee.
“There are always ways we can improve our processes,” Prescott said. “We must continually work toward delivering higher levels of service to our constituents.”
One of LEAN’s main objectives is to shorten the time between when a product or service is requested and when it is delivered to the customer.
“Organizations with the shortest lead time are positioned to be the most credible, which makes them trustworthy through the eyes of the customer,” Prescott said. “By reducing lead time, the department will improve productivity, quality and delivery performance, while reducing inventory and capital expenses.”
LEAN characterizes all activities as either value-added or non-value-added activities. Value-added activities increase value to the customer by transforming information or materials into products and services the customer wants. Non-value-added activities do nothing for customers. They include operations that consume resources, but don’t transform the product or service.
Everything a business provides to its customers that they do not perceive as value is waste, according to Meg Tilley, LEAN Program manager. There are seven wastes that can be identified as common steps within any operation that add no value for the customer:
- Overproduction—work produced before the customer wants it; producing more work than is needed.
- Waiting—idle time created when material, information, people or equipment is not ready.
- Transportation—issue that occurs when materials or work are moved from one location to another.
- Processing/over processing—any operation or process step that does not add value.
- Inventory—more supplies, materials or work on hand than is currently needed.
- Motion—any movement of a person that does not add value is wasted motion.
- Defects—work that contains errors, rework, mistakes or lacks something that is necessary.
“By improving in these key waste areas, the department can move closer to producing exactly what the customer wants, when they want it and in the smallest possible quantities,” Prescott said.
Employees who would like to learn more about Enterprise LEAN can attend one of six day-long, introductory workshops being offered in 2011. The first workshop will be held March 30 in Owatonna. Supervisor approval is needed to participate.
For more information on the Enterprise LEAN initiative and division directors’ IT process, visit ihub.dot.state.mn.us/lean/.
|