The Ombudsman’s Office recently released its first annual report, which features an overview of the program and information collected since the office’s inception in late 2008 through the end of 2009. Deb Ledvina, Mn/DOT ombudsman, leads the office, which features two other full-time employees and various part-time contributors who aid the department in handling complaints about transportation issues.
The report includes a breakdown of:
- The total number of cases by district
- Methods used by parties for contacting the Ombudsman’s Office
- Various issues reported by parties
- How issues were managed and by whom
- How issues were resolved
- How the issues affected the department
In its first 15 months, the office handled more than 150 contacts, of which 113 became cases with the ombudsman.
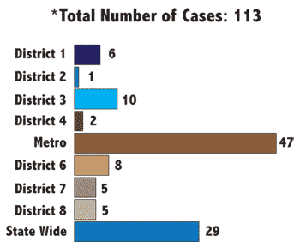
The case numbers reflect calls made to the ombudsman from October 2008 through December 2009. |
“We heard from individuals, city councils and unions regarding concerns each felt needed additional attention,” said Chris Moates, assistant to the transportation ombudsman. “In some cases, the contact came directly through our Web site—other cases were referred by individuals and came in through the districts, Legislature or governor.”
Of the 113 cases, roughly 20 percent were informational requests that required a response from the ombudsman or district office experts.
“Most of the informational cases were requests for easily obtainable information,” Moates said. “None of the issues needed further fact finding beyond the initial information provided to the party.”
The second most common group of cases were about project planning, programming and design, which all together accounted for 13 percent of the total number of cases.
“In addition to those two cases, we dealt with damage, contractor and consultant issues, right of way and MnPASS accounts,” Moates said.
For the majority of cases, the Ombudsman’s Office scours the agency for facts and information to determine the best options for a possible resolution. About 43 percent of all cases are handled via “shuttle diplomacy,” a process where negotiations are conducted by an official who works back and forth between conflicting parties.
Thirty seven percent of all cases were referred to department experts or other agencies. The Ombudsman’s Office often determines quickly if there are experts, internal or external, who are best suited to address the concern, according to Moates.
“Roughly 38 percent of all referred cases were passed on to district office experts, while 34 percent were sent on to other state agencies,” Moates said.
Eighteen of the 113 cases resulted in a change or modified decision, including one case that triggered legislative discussion and resulted in a policy change.
In that lone policy-changing case, the ombudsman received communication from a legislator indicating that a Mn/DOT district had denied a request for right-in access to a constituent’s business. The ombudsman took action by speaking with the business owner and the district and sought clarification of safety and access issues with Mn/DOT experts. After research concluded, department safety and access experts concurred with the district’s decision, which was then supported by the ombudsman. The case ended up triggering a legislative discussion on access control, including a proposal for Mn/DOT to perform benefit-cost analysis on all access request denials.
So far in 2010, the Ombudsman’s Office has handled 138 cases, half of which have required a significant amount of time gathering information, according to Moates.
“We learned a lot in 2009 and added some new personnel to aid in the continuing effort to help the public and department resolve issues and avoid potential problems,” Moates said. “As a team, we will continue to help the department act with integrity and accountability.”
The full 15-page report, including real case scenarios that took place during the program’s first 15 months, will be available soon on the Ombudsman Web page. For more information on the Ombudsman program, visit http://www.dot.state.mn.us/ombudsman/ or read Transportation ombudsman provides custom tailoring when one-size-fits-all doesn’t work, by Deb Ledvina.
How cases affected Mn/DOT
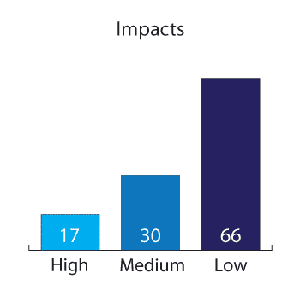
*Determining impact is done by judgment.
|
High Impact Cases:
- System-wide issues (other than MnPASS)
- Multiple parties involved
- Multiple issues (e.g. maintenance, post construction, etc.)
- Potential damage
- Potential high cost (more than $100,000)
- Potential to miss project deadlines
- State and/or congressional political involvement
Medium Impact Cases:
- May impact one or more parties
- Moderate cost in agency time
- Moderate cost in funds (less than $100,000)
- Local political involvement
Low Impact Cases:
- Information or education only
- Single party
|
|
|